Metal Stamping Service
Precision Metal Fabrication Specialist
Home > Capabilities > Metal Stamping Service
Metal Stamping Service
Precision metal stamping offers a fast, cost-effective solution for producing highly accurate parts. PenJing specializes in precision stampings, prioritizing quality for various industries. Our process begins with a custom design considering even the smallest details and strict tolerances. We develop stamping dies at our facility, allowing for efficient production. These die-feed flat sheet metals are then cut into precise stampings. The final shape can be achieved through single-step automation or progressive die operation. PenJing delivers quality metal stamping service.

- Expertise: With over 15 years of experience in precision metal stamping, PenJing is recognized as an expert in the field. Our skilled design engineers and die technicians are among the best in the country.
- Quality Focus: We understand that the success of a product often relies on the quality of its metal stampings. PenJing is committed to delivering power, flexibility, quality, and reliability to meet the manufacturing requirements of our customers.
- State-of-the-art Technology: Our use of state-of-the-art design concepts and processing technology ensures that every precision metal stamping is executed accurately and with consistent quality. Regardless of order size, we strive to deliver excellence.
- Consistency: PenJing guarantees that each batch of precision metal stamping parts can be executed accurately and with consistent quality. Our dedication to accuracy and consistent quality is unwavering, providing customers with dependable products.
Normal Materials used
- Steel: Steel, particularly cold-rolled steel, is a widely used material in precision stamping. It offers excellent strength, durability, and versatility. Different grades of steel, such as stainless steel, high-carbon steel, and low-carbon steel, are chosen based on factors like desired hardness, corrosion resistance, and formability.
- Aluminum: Aluminum is another popular material in precision stamping due to its lightweight properties, corrosion resistance, and good conductivity. It is commonly used in industries like automotive, aerospace, and electronics.
- Copper: Copper is often chosen for precision stamping applications that require excellent electrical conductivity, thermal conductivity, and corrosion resistance. It is commonly used in electrical components, connectors, and heat sinks.
- Brass: Brass, a combination of copper and zinc, is known for its enhanced corrosion resistance, low friction properties, and attractive appearance. It finds applications in areas like plumbing, hardware, and decorative components.
- Nickel and Nickel Alloys: Nickel and its alloys, such as nickel silver, are used when high strength, heat resistance, and corrosion resistance are required. They are commonly used in industries like electronics, telecommunications, and automotive.
- Precious Metals: In certain high-end applications, precision stamping may involve precious metals like gold, silver, or platinum. These materials are chosen for their unique properties and aesthetic appeal.
Industries We Served
- Automotive Manufacturing
- Precision Medical Devices
- Power Transmission Equipment
- Motor Control
- Precision Elevators
- Consumer Electronics
- Hydrogen Energy
- New Energy Vehicles
- Mechanical Equipment Seals
- Power Supply
Finished Products Gallery

Laptop TP Module

Medical Devices

TP Touch Screen
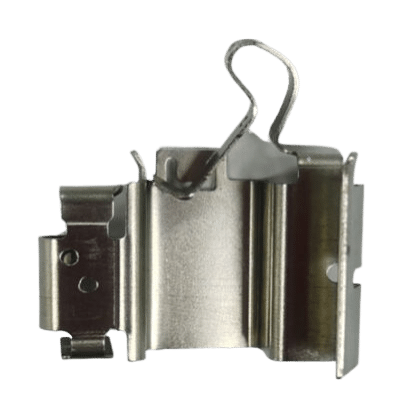
Brake Pad Circlip

Electrocar Motor Parts

Laptop Radiator

Laptop Back Panel
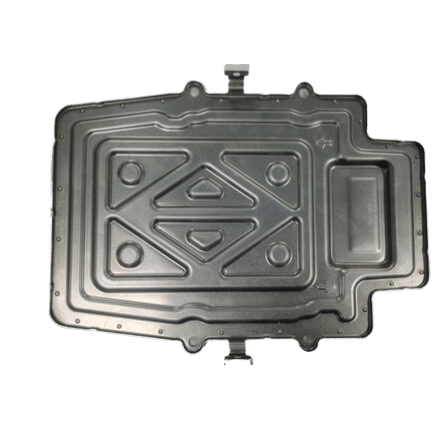
Motor Controller Cover
Various Operations In The Stamping Process
- Blanking: Cutting out a flat shape from a sheet metal using a die, creating a blank for further processing.
- Trimming: Removing excess material or unwanted edges from a stamped part to achieve the desired shape and dimensions.
- Shaving: Precision trimming of the surface of a part to remove imperfections or excess material.
- Cutoff: Separating a part from the surrounding material or from a larger strip of metal.
- Shearing: Cutting a straight line through a sheet metal to create separate pieces.
- Piercing: Creating holes or openings in the metal by punching it with a specialized tool.
- Slitting: Cutting a long strip of material into narrower strips, typically done in a continuous process.
- Perforating: Creating a pattern of small holes or perforations in the material for ventilation, filtration, or decorative purposes.
- Lancing: Making a partial cut or indentation in the metal to create a bendable tab or feature.
- Extruding: Forcing the metal through a shaped die to create a continuous profile or complex shape.
- Notching: Cutting out a small V-shaped or U-shaped notch in the edge of a part to facilitate bending or assembly.
- Nibbling: Producing a series of closely spaced cuts or notches in the material to remove small sections and shape the part.
- Bending: Deforming the metal to achieve the desired angle, curve, or shape using specialized tools or dies.
- Forming: Shaping the metal into a three-dimensional form, such as curves, flanges, or embossed features.
- Squeezing: Compressing the metal between two dies to create intricate shapes or to join multiple pieces together.
- Drawing: Pulling the metal through a die to reduce its diameter or thickness while increasing its length, often used for creating tubes or cylindrical shapes.