Laptop Metal Parts
Precision Metal Fabrication Specialist
Laptop Metal Parts
Precision metal stamping parts for notebook computers demand rigorous standards in mold accuracy, materials, surface treatment, production processes, and final inspections.
- Mold Accuracy: Tolerances for these parts are minimal, often in microns. Precision moulds ensure the exact replication of the design, minimizing errors.
- Materials: High-quality materials like aluminum or stainless steel are preferred for their durability and lightweight properties. These materials must adhere to strict industry standards for strength and conductivity.
- Surface Treatment: The surface finish is crucial for aesthetics and functionality. Anodizing or electroplating is commonly used to enhance corrosion resistance and improve appearance.
- Production Process: The stamping process requires precision machinery to cut, bend, and shape the metal sheets accurately. Tight controls on temperature, pressure, and tool wear are necessary.
- Finished Product Inspection: Rigorous quality checks, including dimensional measurement, surface finish analysis, and material testing, guarantee the parts meet specifications. Components must also be checked for compatibility and assembly integrity within the notebook.
These requirements ensure that precision metal stamping parts not only meet design specifications but also contribute to the overall performance, reliability, and aesthetics of modern notebook computers.
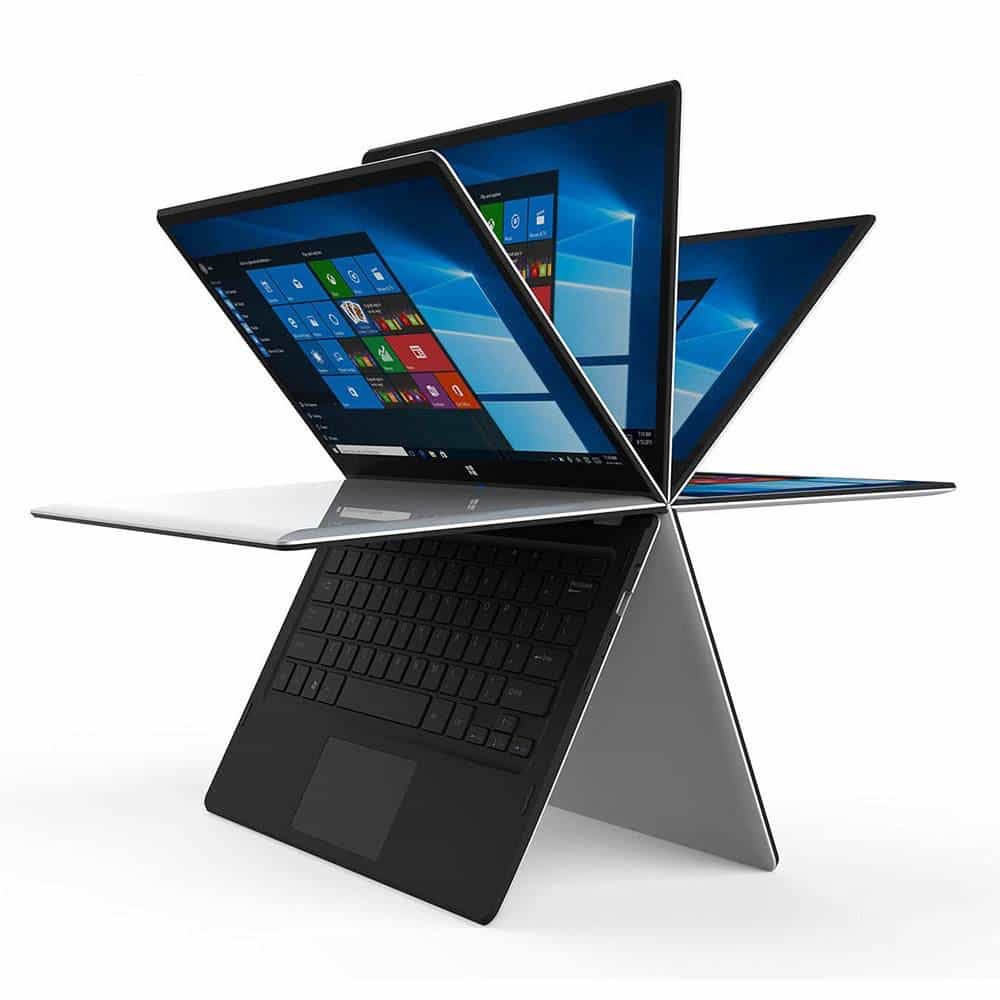
Stamping Materials Used
- SGCC Galvanized Iron (0.3 – 1.2mm)
- Stainless Steel SUS304(0.1 – 0.8mm)
- Aluminum (0.3 – 0.6mm)
- Copper (0.1 – 0.5mm)
Stamping Surface Treatment
- Spraying
- Electrophoretic Printing
- Sand Blast Oxidation
- Electroplating
Features
Product features: Various precision built-in functional parts, appearance parts, product materials involving galvanized iron SGCC, aluminum , stainless steel SUS304, copper, etc., equipment and mold accuracy to ensure a high production accuracy and productivity, The product process covers stamping, grinding, polishing, tapping chamfer, heat treatment, electroplating, spraying, electrophoretic printing, sand blast oxidation, welding and so on.
Finished Products Gallery

Laptop TP Module

Laptop TP Module

TP Touch Screen
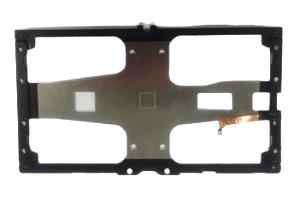
TP Touch Screen
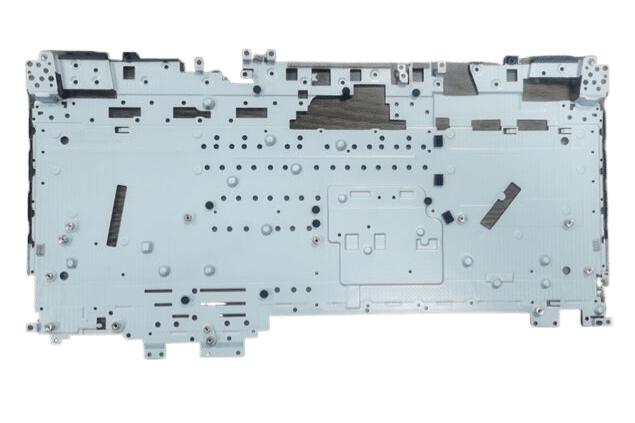
Laptop Back Panel

Laptop Radiator

Laptop Back Panel
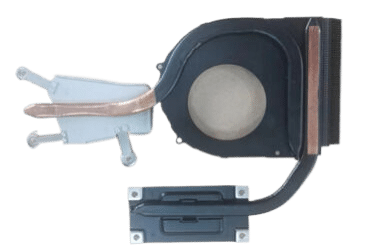