Solution
Precision Metal Fabrication Specialist
Home > Solution
One-Stop Custom Metal Stamping Solution
PenJing provides a one-stop solution for customers starting from demand analysis, die design and manufacturing, stamping parts production management, finished product qualification inspection, international transportation and delivery to customers’ overseas warehouses, we care what you care!
Understanding customer requirements and gathering detailed information about technical requirements and quality standards
Considering the durability and ductility of the mould material to ensure the machining accuracy when design the initial mould.
Procuring high-quality raw materials to conduct precision stamping while following safety and quality standards
Implementing five quality tools to ensure and comply with customer drawing requirements.
Testing packaging methods, planning transportation routes, modes and schedules to meet all customer's requirements.
Customer Demand Analysis:
- Understanding Customer Requirements:
In-depth dialogue, synchronous FMEA analysis, fully understand customer’s specific needs. This includes the technical requirements and quality standards of the product. The goal is to communicate deeply with customers through the whole process and build a comprehensive customer profile.

- Market Research: Beyond the immediate customer request, it’s important to delve into broader market trends. Research competitors’ offerings, customer preferences, and emerging industry technologies. This helps identify potential future demands and opportunities for innovation.
Attention: Maintain a proactive and open channel of communication with customers throughout the project. Be ready to accommodate reasonable changes or adaptations to the project scope. Accurate documentation of customer requirements is essential to avoid misunderstandings and disputes.
Mold Design and Production:
- Concept and Design: The design phase involves creating a detailed plan, considering the durability and ductility of the mold material, and ensuring machining accuracy to develop the initial mold concept and design. Collaboration between design and engineering teams is crucial to ensure that the design is both innovative and manufacturable.
- Prototyping: Prototyping is a critical step for testing and validating the design. Conduct feasibility studies, make rapid prototypes, and perform functional tests to ensure that the mold design is optimal.

- Production: During production, focus on quality control and consistency. Regularly inspect and maintain machinery, and ensure that the workforce is well-trained and skilled in the use of tools and equipment.
Attention: Implement robust version control for design documents to track design changes and maintain design integrity. Maintain strict quality control standards throughout the manufacturing process, conducting inspections at various stages to minimize defects.
Stamping Production Process:
Material Sourcing: Carefully select suppliers that provide high-quality raw materials, and establish long-term partnerships to ensure a consistent supply. Conduct regular quality audits of material suppliers.
Stamping Operations: Stamping operations should follow strict safety protocols. Regularly train operators in safety measures and provide ongoing education on precision techniques.

Quality Control: Implement a comprehensive quality control process, including real-time monitoring of critical parameters, inspection of finished products, and testing for durability and quality standards adherence.
Attention: Establish preventative maintenance schedules for stamping equipment to minimize downtime and ensure precision. Conduct regular safety audits to maintain a safe working environment.
Product Qualification Inspection:
Inspection: Inspection should be systematic, with defined criteria for different product features. Inspectors should be well-trained in recognizing defects and variances, and there should be a clear process for handling non-conforming products.
Testing: Depending on the product, conduct various tests to ensure quality and reliability. This could include stress tests, environmental tests, or dimensional accuracy tests.
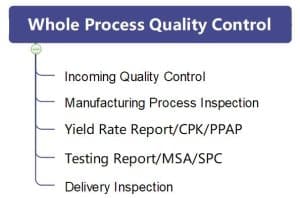
Documentation: Maintain meticulous records of inspection results, testing outcomes, and any deviations from the expected standards. This documentation is invaluable for traceability and continuous improvement efforts.
Attention: Regularly calibrate inspection equipment to maintain accuracy. Develop a robust non-conformance reporting system to address and learn from quality issues.
International Transportation to Overseas Customers' Warehouses:
Logistics Management: Create a comprehensive logistics plan that includes route optimization, mode selection (air, sea, land), and scheduling. Efficiently manage inventory levels to avoid overstocking or understocking.
Customs Compliance: Ensure full compliance with international trade regulations, including customs documentation, duties, and import/export requirements. Stay informed about changes in international trade laws.
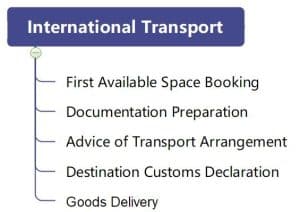
Delivery Tracking: Implement a robust tracking system to monitor the movement of goods in real-time. Provide customers with regular updates on the status of their shipments to enhance transparency and trust.
Attention: Develop contingency plans for unexpected events, such as customs delays, transportation disruptions, or adverse weather conditions. Establish a risk management team to proactively identify and mitigate potential logistics risks.